The Titan Structure - In conversation with Head of Manufacturing - Paul Cawthorne
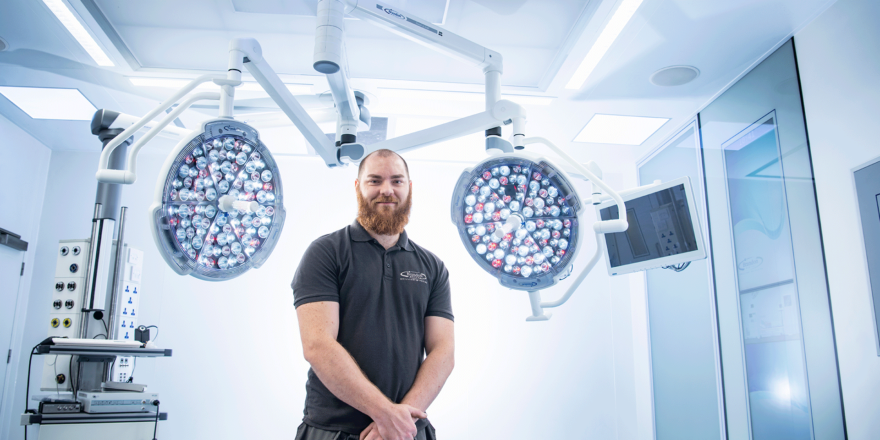
In your own words, what is the Titan Structure – how would you describe it to someone who knows nothing about it?
The Titan Structure is the new design for our central axis system. In other words, the primary fixing from which we are able to hang/attach all our operating lights or other products, such as monitors. There are several new features within the Titan Structure design, such as improved agility and easier installation (from a two-man to a single-man job), as it is more lightweight than the previous Mk IV central axis. Titan has also enabled a large cost reduction.
What was your personal role/how were you involved within the Titan Structure project – what were your responsibilities?
I oversee the manufacturing of products therefore, in the Titan Structure project, my responsibilities came after the Titan Structure had been designed; I had to deal with potential problems and take the design engineer’s concepts and ideas from CAD and turn them into a physical, real-life product through managing my team and the various jobs we do.
During the Titan Structure project, have you worked in a team or individually – do you prefer group projects or working by yourself, and do you think there should be more teamwork within projects?
I definitely believe there should be more teamwork within projects at Brandon Medical as it allows different teams to transfer their specific skills to other departments. For example, with the involvement of both my team in manufacturing and the team in production and me were able to give the design engineers helpful input through the insight we had into the Titan Structure’s physical movements and behaviour.
Within the project, I was able to work in multiple teams as I worked within my manufacturing team and also closely with the production team and (towards the end) with the design team – which was very enjoyable from a social perspective and for the improved outcome of the product.
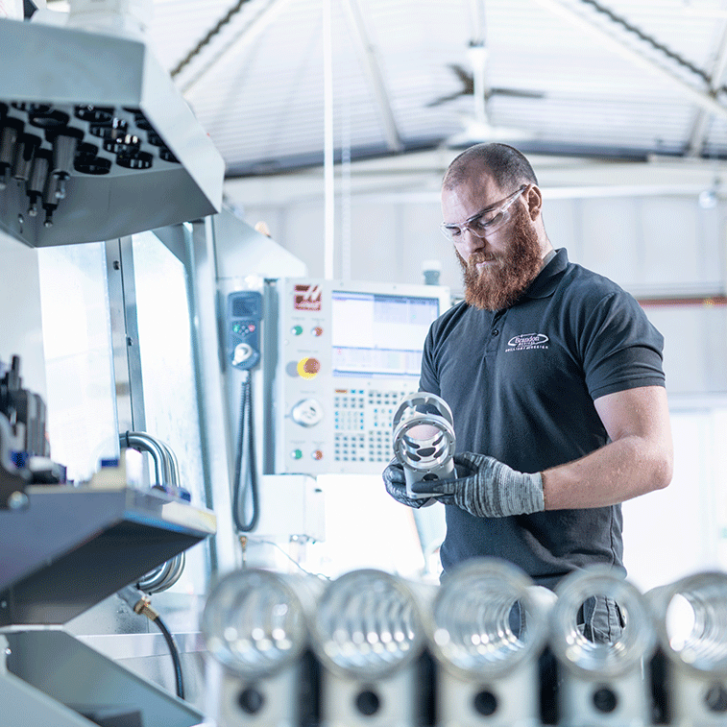
The Titan Structure is the new design for our central axis system. In other words, the primary fixing from which we can hang/attach all our operating lights or other products, such as monitors.
There are several new features within the Titan Structure design, such as improved agility and easier installation (from a two-man to a single-man job), as it is more lightweight than the previous Mk IV central axis. Titan has also enabled a large cost reduction.
The Titan Structure project was a large-scale project – do these projects ever feel overwhelming and if so, how could we improve how we run new product development projects at Brandon Medical?
For the most part, no the Titan Structure did not feel like an overwhelming project due to the fact that it was solved in little parts, with all design, manufacturing and production teams working together to complete the jobs therefore, our smaller sections did not feel as impossible.
However, the project was started during COVID-19 therefore, on occasion, it was difficult to communicate with different teams; it was only this inability to communicate that sometimes made our tasks feel much larger and overwhelming.
What was your favourite part of the Titan Structure project what was the most challenging part of the Titan Structure project for you?
The Titan Structure project was an enjoyable project to be part of – especially as there were very few issues or dilemmas that occurred within manufacturing. However, one of the more challenging aspects of the project was the problem with castings on the arm of the structure, which was later solved with a new machine. This machine solved the issue as it was able to cover every surface at once in one single operation.
Do you think the Titan Structure project was a smooth, easy project or were there problems and issues along the way and, if so, how did you and your team manage these problems?
Although I am sure other teams, such as design, had many issues and problems that needed to be fixed or altered, for me and my manufacturing team there were very few problems that needed to be solved. There were very minor teething problems, however, this is to be expected within the manufacturing process and aspects need adapting or changing slightly but, overall, the project was relatively smooth sailing.
What were the aims of this project and do you think you, and your team, achieved these aims?
Our aims, within the broader aims of the Titan Structure project, were to enable it to lose weight and allow it to retrofit different adaptors to it; both of these core aims were fulfilled therefore I think the project was successful.
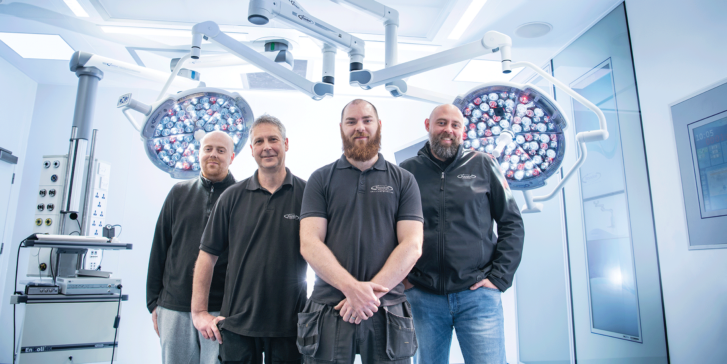
More information about the creation of the Titan Project.
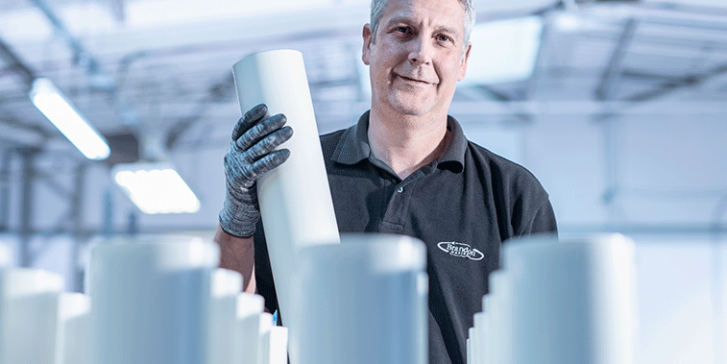
In conversation with Head of Production, James Bates, on his experiences with the Titan Project.
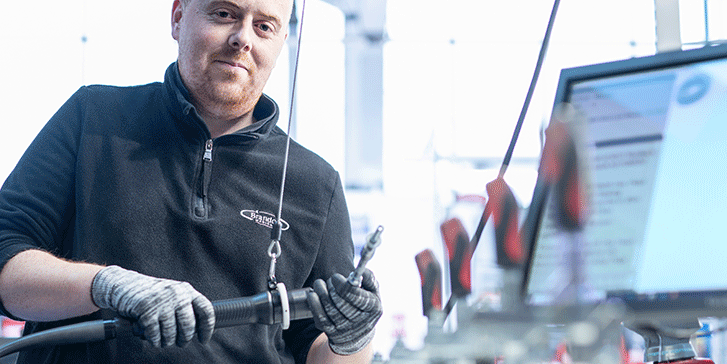
Learn more about Jack’s experience as part of the team creating the new Titan Project.
Recent articles

Brandon Medical Welcomes Mayor Tracy Brabin for the Launch of West Yorkshire’s £160 Million Investment Zone
Brandon Medical Welcomes Mayor Tracy Brabin for the Launch of West Yorkshire’s £160 Million Investment Zone
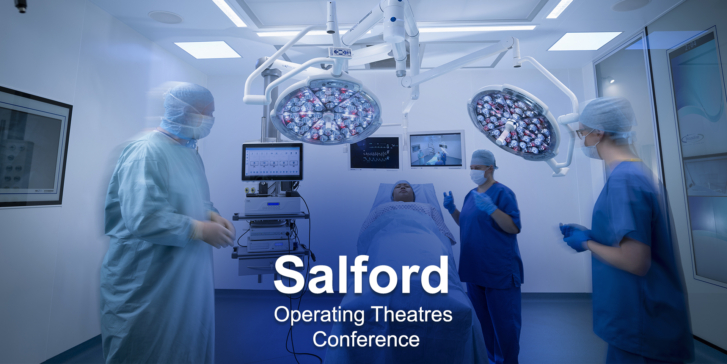
Salford Operating Theatres Conference 2025
Brandon Medical Returns to The Operating Theatres Conference: Explore Integrated Solutions for Acute Care Areas

Arab Health 2025
Arab Health 2025: SMART healthcare spaces: ready now and future-proof